Builder
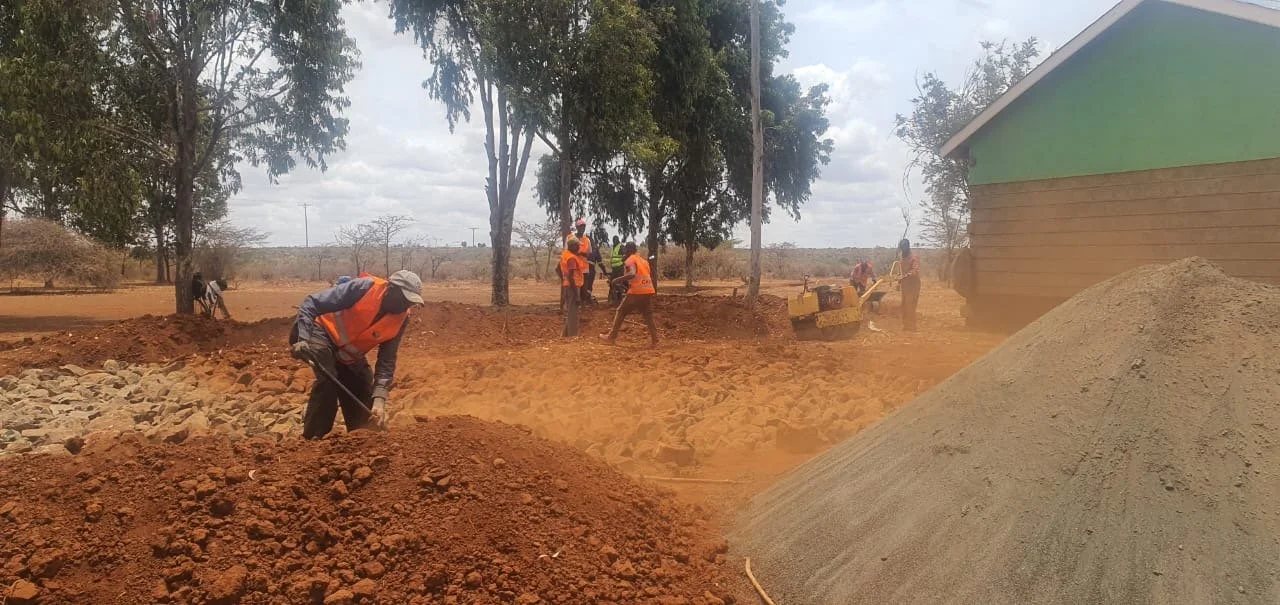
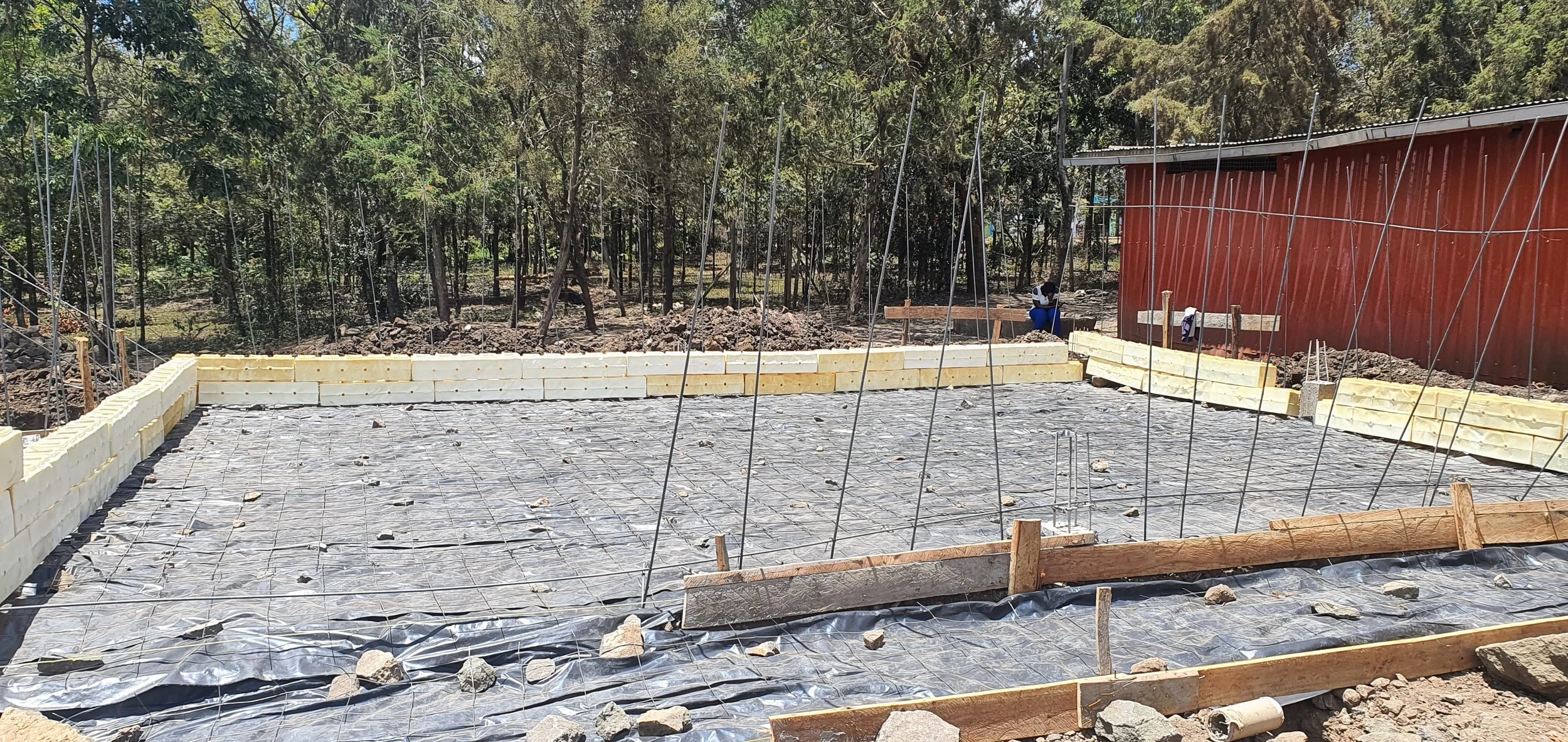
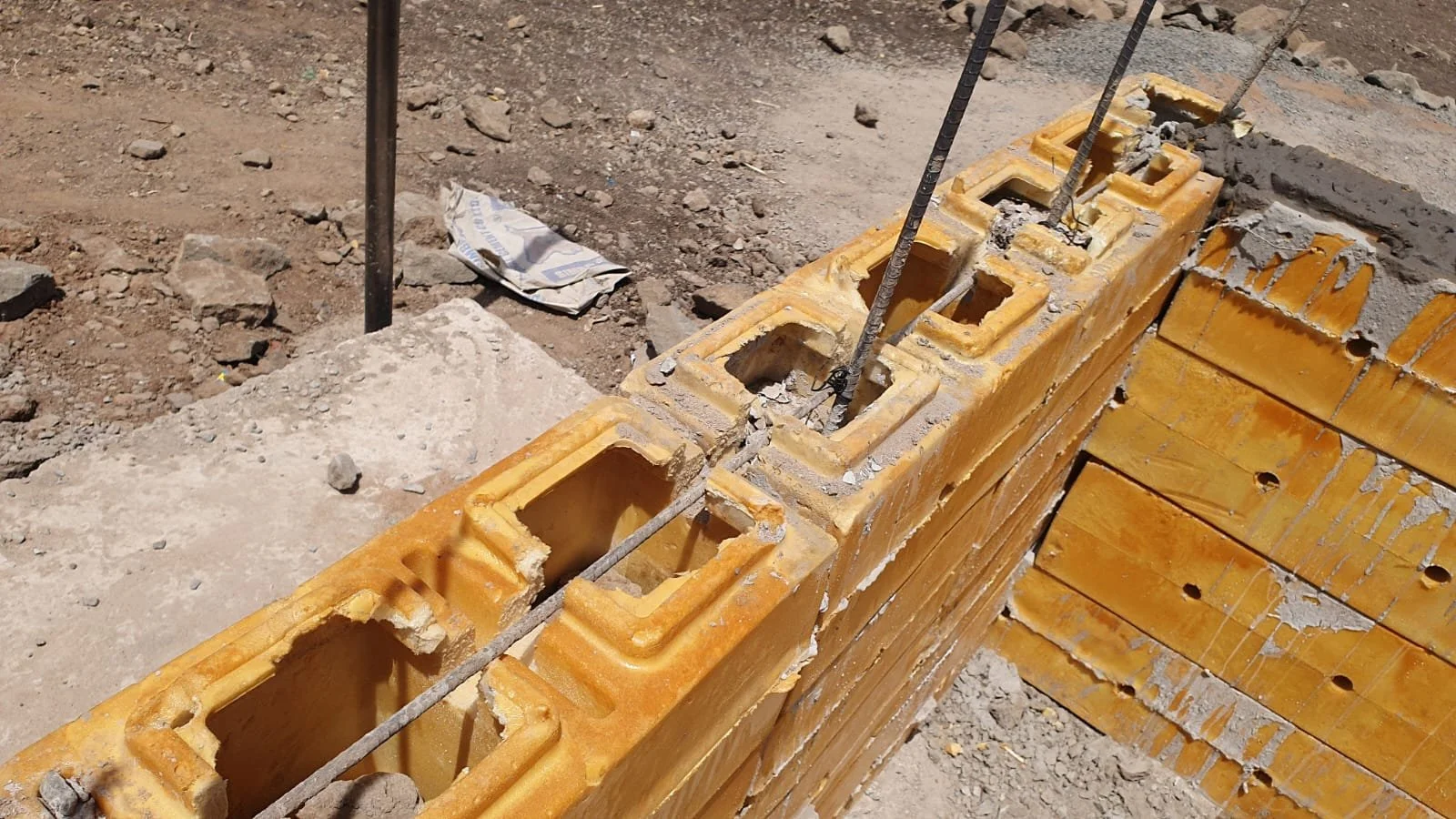


Cost Effective. The Onsite ICF Block system offers licensed builders a cost-effective, high-performing solution with quick project turnaround from start to finish, ensuring both profit improvement and project-level cost savings. Maximize your investment—build more high-quality homes per dollar spent. Boost your profitability and enhance your competitive edge in securing projects. With a modest capital investment and a solid ROI, the system is ideal for mid-size contractors and owner/operator dealers seeking a scalable, efficient solution.
Fast: More houses in less time with less people. Reduce delivery time of the project from start to finish. Construction of the walls for a typical project can be done in less than a week. Productivity is high. Projects stay on schedule and avoid costly delays. The block making system is efficient and can be conveniently done on site. Blocks can be made and used same day or made in advance.
Convenient. This system goes anywhere. Mobile factory can fabricate blocks in remote and undeveloped areas, giving those communities access to better housing. Material requirements are minimal, compact, easy to transport.
Simple. This is a very simple walling system. Stacking blocks is easy and fast. No mortar is required. Filling out the columns is basic and repetitive work. It can be done with unskilled labor under the supervision of a trained foreman. Simplicity solves skilled labor shortages, shortens training, reduces overall staff and produces a consistent final product.
Lightweight: The low weight of the blocks (~1kg) means less fatigue for the workforce, facilitates the employment of women, allows for tools that are simple, clean and quiet and improves safety and satisfaction on the jobsite compared to traditional methods involving bricks or concrete. In addition, the lightweight structure reduces foundation design requirements.
Superior. The finished product creates a comfortable place to live, gather, learn or work. Walls are strong, weatherproof, pest resistant and fireproof. The insulation provided by the foam reduces heat stress and increases comfort. The durable structure can be built to withstand natural disasters. The insulated walls improve the sound-reduction within the building. Safety, security and appearance are additional factors that will attract buyers and tenants quickly.
Here’s how it goes together:
Foundation and floor. It is always necessary to make a solid foundation that will withstand local conditions and support the structure. Providing a concrete floor is best practice but can be optional if resources are limited.
Rebar structure. Rebar is critical to achieving the strength and safety of the ‘post and beam’ construction. Rebar should be anchored to the foundation at locations that will align with the cores of the block, spaced at every third core or as required for structural strength.
Blocks: Blocks are threaded over the rebar and stacked into place. The interlocking of the blocks ensures a proper fit. Joints are staggered with each layer. Some blocks are easily cut to fit.
Concrete reinforcement: Concrete is poured into the cores with rebar.
Ring Beam: a horizontal beam is created at intervals as required and at the top. The blocks are trimmed to create a trough, rebar is laid and linked to vertical rebar, then the trough is filled with concrete. This creates the interconnected post and beam skeleton of reinforced concrete.
Walls: Blocks and rebar are progressively placed to the desired height of the wall. A ring beam is used at the topmost layer. Blocks on the end walls are placed in a pyramid fashion to form the peak.
Surface finishing: Foam block surfaces are typically covered by either stucco or plaster and then painted. In the finished product, the foam is not visible and is not exposed to weather or wear and tear.
Roof: The roof is constructed in the usual fashion. For the most comfortable condition, we recommend roof trusses, with batting insulation on the lower portion followed by a hard ceiling surface. Other means for insulated roofing are under development.
Windows and more: Windows, doors, and trim features are added in the usual manner.
Compliance: Most importantly, comply with local building codes and standards. Part of the beauty of the foam block is how easily it conforms to known methods.
Business Partnerships
We believe that the path to scale runs through entrepreneurs and private enterprise. Becoming a License Builder with Onsite ICF can drive growth and profitability in your business.
CONSIDER THE BENEFITS
Easy to work with: The foam blocks are easily integrated into existing construction methods and standards. Design costs are minimal.
Reduced labor costs: Fit and finish of the blocks ensures a professional result while simplifying the required skill level of the work. Labor costs are reduced.
Portable: Portability of the Onsite RIM™ system and chemicals simplifies the transportation and logistics costs compared to other methods. Freight costs are reduced.
Potential revenue: Block production creates value, which increases the potential for revenue. Save costs, earn more.
This is a better house: Stronger, safer, more comfortable, and more durable than other houses, which means satisfied customers. This is win-win.
We invite inquiries from businesses interested in becoming Licensed Builders with the Onsite RIM system. Contact your Region office to discuss opportunities.
Simple. Beautiful. Comfortable. Durable.
Design
Use your imagination. Options are limitless, but we have a growing library of standard floor plans. Construction detail views are also available.
Training and Support
We provide training for new users which may be either live remote or on site.